Aiming high: Australia makes world’s first 3D-printed jet engines
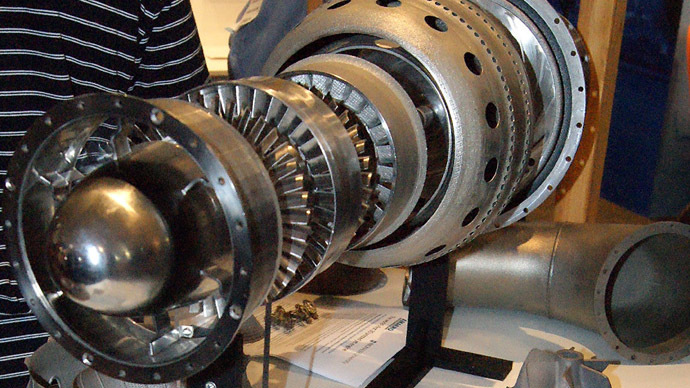
Australian researchers have created two jet engines using 3D printing, a breakthrough that proves the technology can create high-quality products from a variety of metals.
Using a gas turbine engine as a template, researchers from
Melbourne's Monash University, and staff from the CSIRO and
Deakin University, congratulated themselves for successfully
printing an “aircraft quality” product, which could
revolutionize the way aircraft are built in the future.
"The significance... is the recognition by major
manufacturers and engineering companies like Safran and Airbus
that the material you can print using 3D metal printing is of
aircraft quality and I think that's hugely significant,"
Monash university's vice provost for research, Ian Smith, told
AFP.
"It's a disruptive technology. We've seen a lot happening in
the plastics and polymer space, but this is exciting because it's
now metals and light metals and things like titanium, nickel and
aluminum."
3D printing can slash production times from three months to just six days, researchers say.
READ MORE:Chinese firm 3D-prints 5-story house using construction waste 'ink'
Xinhua Wu, director of the Monash center for additive
manufacturing, said her team tediously scanned the separate parts
of the template engine, with the project taking about one year to
finish.
One of the jet engines is on display at the Australian
International Airshow in Melbourne with the other being featured
in Toulouse at the French aerospace company Microturbo.
Smith predicted the new technology could be used to build a
variety of customized parts quickly and cheaply, specifically in
the field of medicine.
"Where we see some of the big opportunities are in the
medical space where you can make bespoke parts for the body –
replacement joints and hips designed specifically for that
individual," he said.
"A lot of surgeons want to make their own instruments that
are customized for them or a particular surgical procedure."
Engineers at Monash University have teamed up Amaero Engineering,
the private company established by Monash to deliver the product
to market. The Monash-led research group is making top-secret
prototypes for Boeing, Airbus, Raytheon and Safran in a move that
could be the “savior of Australia's struggling manufacturing
sector,” Reuters reported.
READ MORE: Breaking convention: New 3D food
printer makes edible cookies
"This will allow aerospace companies to compress their
development cycles because we are making these prototype engines
three or four times faster than normal," said Simon
Marriott, CEO of Amaero Engineering.
Marriott said his company wants the 3D-printed engine components
in flight tests within the next year and licensed for commercial
application within the next two to three years.
Australia, which has one of only three large-format 3D metal
printers in the world (France and Germany have the others) is in
a position to corner the market on the new technology, providing
a much-needed boost to its economy.
Market researcher Gartner forecast in 2014 that global spending
on 3D printing will surge from $1.6 billion in 2015 to about
$13.4 billion in 2018.
Around since the 1980s, products created by 3D printing
technology have included everything from bikinis to assault
weapons.